The ground level power supply (APS) system for the electric road, a technology of the future
The eRoadMontBlanc project is based on the ground-level power supply system (in French: alimentation par le sol – APS) developed by Alstom in the early 2000s for trams and has been adapted for road use. The principle is simple: a conductive rail inserted into the carriageway, flush with the ground, captures the current under the vehicle, using a mobile articulated arm fitted with friction pads that rest on the conductive segments to generate electricity. The stored energy then powers the vehicle for several thousand kilometres without the need to stop to recharge the batteries. This system also enables the development of lighter and smaller batteries at lower cost. The working groups of the French Ministry for Ecological Transition and Territorial Cohesion are assuming that heavy goods vehicles will be equipped with batteries with a capacity of just 350 kWh. This technology makes it possible to validate this assumption and also guarantees that vehicles can be recharged while on the road.
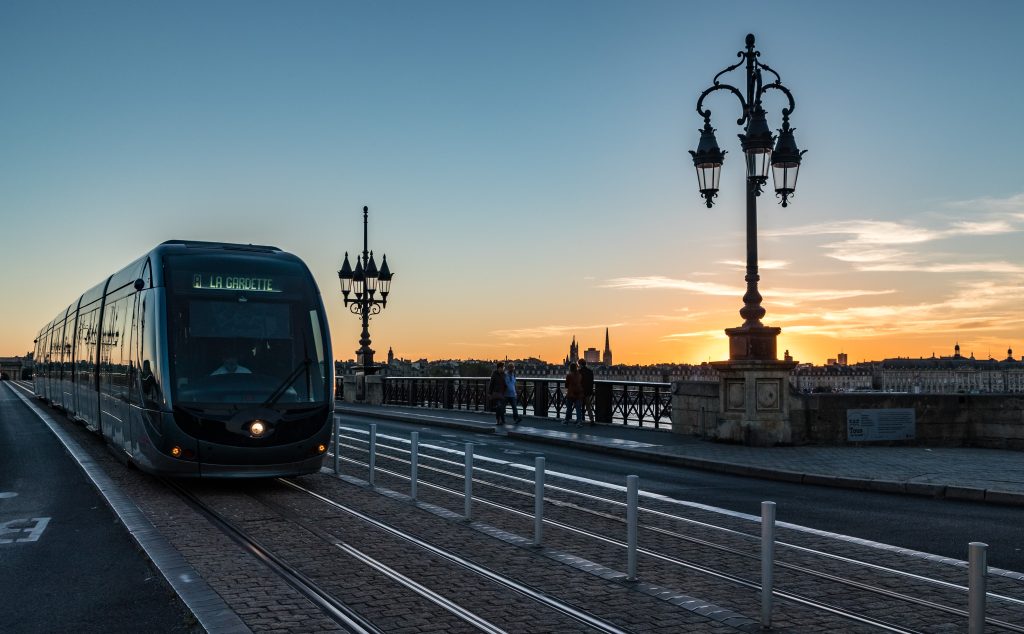
A technology that has already proven itself on trams
The APS solution for the road is based on the ground level power supply system developed by Alstom in the early 2000s to power trams via a conductive rail instead of the conventional overhead contact line.
The system, which has been in service for over 20 years in Bordeaux and now on many networks worldwide, has amply demonstrated its efficiency, availability and safety, with more than 70 million kilometres covered in APS mode. Since then, this principle has been developed for electric charging solutions at tram and bus stops, and for an electric road solution.
Alstom has been working on the electric road solution since 2012 using a demonstrator project on test tracks in Sweden, alongside Volvo Trucks, to show the feasibility of recharging a heavy goods vehicle while in motion. Since 2017, Alstom has been developing a ground level electric charging solution that is truly suited to the requirements of the road.
The challenge of adjusting APS technology to motorway infrastructure
One of the major challenges in adjusting APS technology to roads is integrating the conductive rail into the surface of a motorway.
The conductive rail consists of insulating ERS components made from EPDM rubber, each around 2.7 m long, connected and installed like Lego pieces in a 50 cm wide and 7 cm deep grove, made in the centre of the slow lane. The conductive rail is secured into the road surface using a resin.
This interface between rubber and asphalt has been validated by tests carried out in a laboratory at the Université Gustave Eiffel in Nantes. The tests were conducted using the “FABAC” machine (a small traffic simulator that can reproduce real HGV axial loads on small road boards). They focused on bonding, rutting, thermal reactions and interface fatigue.
Two test tracks were built in 2019 for larger scale validation of two other key components. One on the Nantes campus of the Université Gustave Eiffel, to test the level of grip on the conductive rail of a motorbike and a car. The other in the Vosges mountains, to demonstrate the compatibility and feasibility of the system in winter, through detailed monitoring of snow clearing operation and the effects of the weather and the conductive rail.
Technology with great potential for decarbonising road mobility
Three working groups bringing together the entire ecosystem (transporters, manufacturers, road managers, energy providers, solution manufacturers, etc.) and spearheaded by the Ministry of Ecological Transition and Territorial Cohesion, have examined the potential of the ERS. They delivered their findings at the meeting of the ministerial committee for development and innovation in transport held on 20 October 2021. The findings, which are also included in the reports available on the Ministry’s website, acknowledge that the ground level power supply solution is the best suited to the various requirements based on the latest developments.
- Interoperability and adaptation of the technology to all types of vehicles
- Easy maintenance with minimal impact on the road (no deep escalation) and space required for the infrastructure
- Infrastructure that does not cause visual pollution and allows easy onsite work
- Durability of the system, particularly against extreme weather conditions and heavy traffic
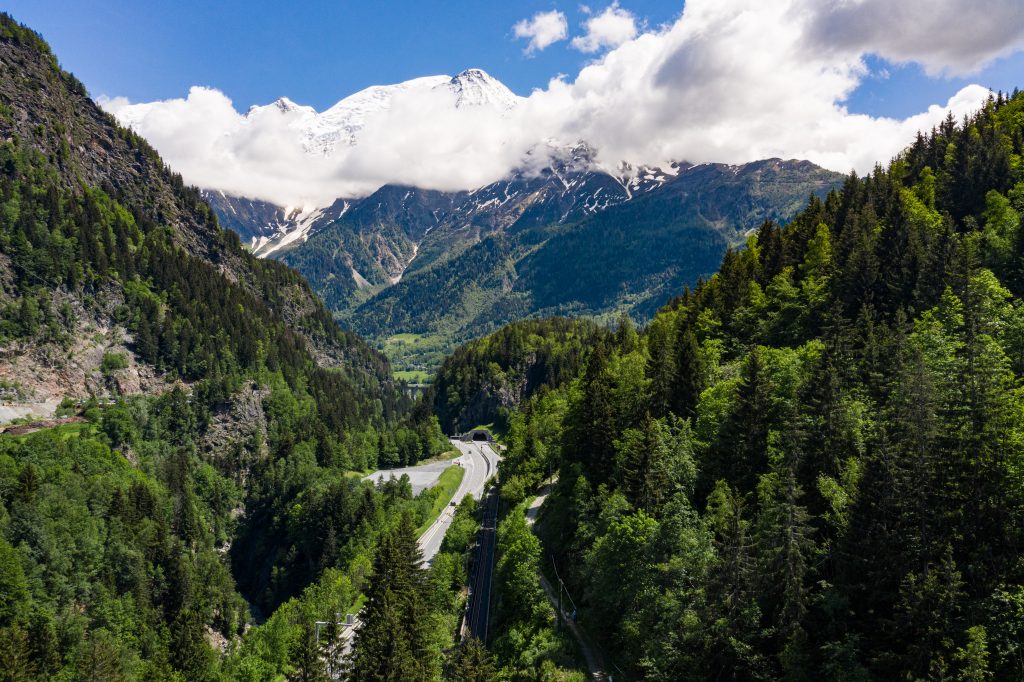